Stainless Steel Gas Struts: The sea, a realm of beauty and relentless force, demands materials that can withstand its corrosive embrace. Within this challenging environment, 316 marine gas struts emerge as the mariner’s steadfast companion, ensuring smooth, reliable operation where lesser materials succumb.

GASTAC, a leading Chinese marine gas struts manufacturer, offers advanced production technology and a skilled manufacturing team. For custom stainless steel gas springs, contact sales@gastac.com. For standard marine gas strut specifications, visit the GASTAC online store for easy purchasing and reliable solutions.
The Chemical Fortress: 316 vs. 304 in the Marine Realm
Compositional Superiority: 316’s marine gas shocks defining feature is the addition of molybdenum, a strategic element that significantly enhances its resistance to chloride ions, the primary aggressors in saltwater corrosion. This element creates a superior protective layer. 304 marine gas springs, while possessing good corrosion resistance, lacks this crucial fortification, making it vulnerable to pitting and crevice corrosion in marine settings.

Why 316 Boat Hatch Gas Struts Endures: In saltwater, chloride ions attack the passive chromium oxide layer on stainless steel. Molybdenum in 316 gas shock for boat hatch strengthens this layer, preventing the formation of pits and crevices that can lead to catastrophic failures.
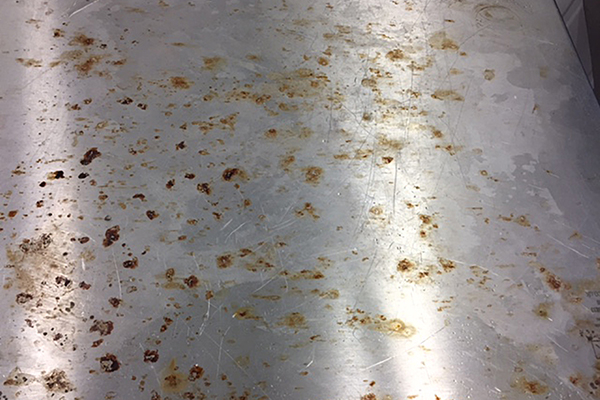
Real-World Marine Applications: Where 316 Reigns Supreme
- Offshore Platforms and Oil Rigs: These colossal structures, constantly battered by waves and salt spray, rely on 316 marine gas struts for access panels, equipment hatches, and safety mechanisms. Their reliability is crucial for maintaining operational integrity and preventing costly downtime.
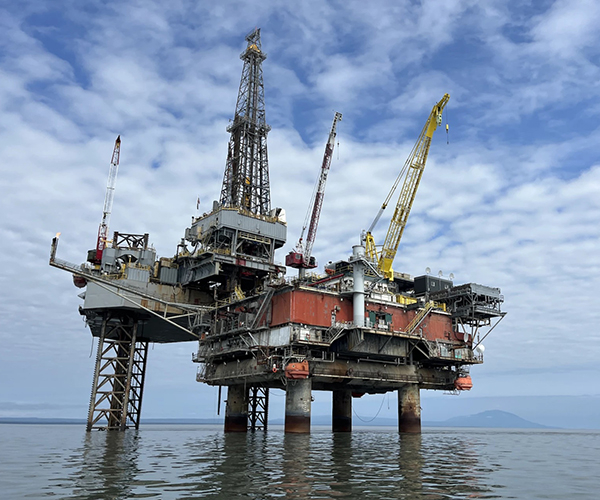
- Luxury Yachts and Sailing Vessels: From hatch lifts and engine compartment access to swim platform controls, 316 marine gas shocks ensure smooth, effortless operation, enhancing the onboard experience and maintaining the vessel’s pristine appearance.
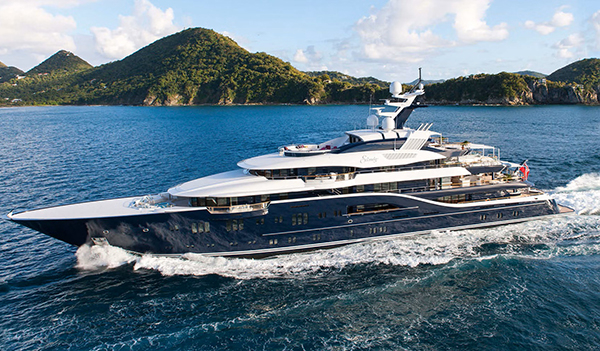
- Commercial Shipping and Cargo Vessels: In the demanding world of commercial shipping, 316 marine gas springs are essential for cargo hatch operations, equipment access, and safety systems. Their durability minimizes maintenance and ensures reliable operation in harsh conditions.

- Submersible Vehicles and ROVs: These underwater explorers, operating in the most corrosive environments, rely on 316 boat hatch gas struts components for their structural integrity and operational reliability. 316 gas struts enable precise control of robotic arms and other critical functions.

- Coastal Infrastructure and Marine Equipment: From dockside access panels to navigational aids, 316 gas shock for boat hatches ensure the longevity and reliability of essential marine infrastructure.
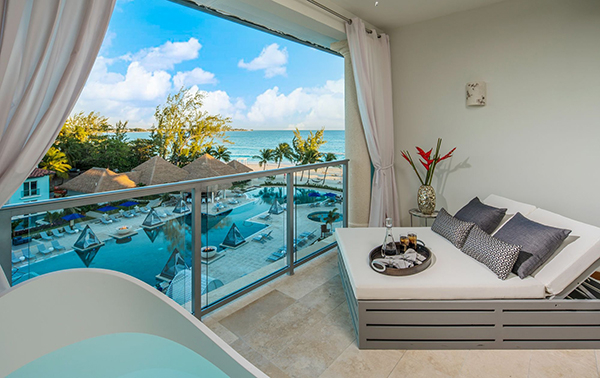
The Economic Advantage: Investing in 316 marine gas struts for Long-Term Savings
- Reduced Maintenance and Replacement Costs: While 316 gas shock for boat hatch may have a higher initial cost, its extended lifespan and superior corrosion resistance translate to significant long-term savings. In the marine environment, where equipment replacement is costly and challenging, 316’s boat hatch gas springs durability is an invaluable asset.
- Minimized Downtime and Operational Disruptions: Equipment failures due to corrosion can lead to costly downtime and operational disruptions. 316 marine gas struts minimize these risks, ensuring uninterrupted operation and maximizing productivity.
- Enhanced Safety and Reliability: In critical marine applications, the reliability of boat hatch struts is paramount. 316’s boat gas struts superior corrosion resistance ensures that these components perform reliably, enhancing safety and preventing accidents.
Pitting and Crevice Corrosion: The Silent Enemies of Marine Equipment
- Understanding the Mechanisms: Pitting corrosion occurs when chloride ions attack localized areas of the stainless steel surface, creating small pits that can propagate and lead to structural failure. Crevice corrosion occurs in confined spaces, such as gaps between fasteners and surfaces, where stagnant saltwater can create a corrosive environment.
- 316’s Resistance: 316’s marine gas struts molybdenum content significantly enhances its resistance to both pitting and crevice corrosion, ensuring long-term protection in marine environments.
- Visual Comparisons: Under a microscope, the differences are stark. 304 stainless steel gas strut displays clear signs of pitting and crevice damage, while 316 stainless steel gas spring maintains a much smoother and more intact surface.
Identifying 316 in the Field: Practical Tips for Mariners:
- Chemical Spot Tests: Chemical spot tests can be used to identify the presence of molybdenum, confirming the presence of 316 stainless steel.
- Visual Cues: While visual inspection alone may not be conclusive, 316 often exhibits a slightly different surface finish compared to 304.
- Material Certifications: Always request material certifications from suppliers to ensure the authenticity of 316 stainless steel.
In the demanding realm of marine applications, 316 stainless steel gas struts stand as a testament to durability, reliability, and long-term performance. Their superior corrosion resistance and robust construction make them an indispensable asset for mariners seeking to navigate the challenges of the sea.